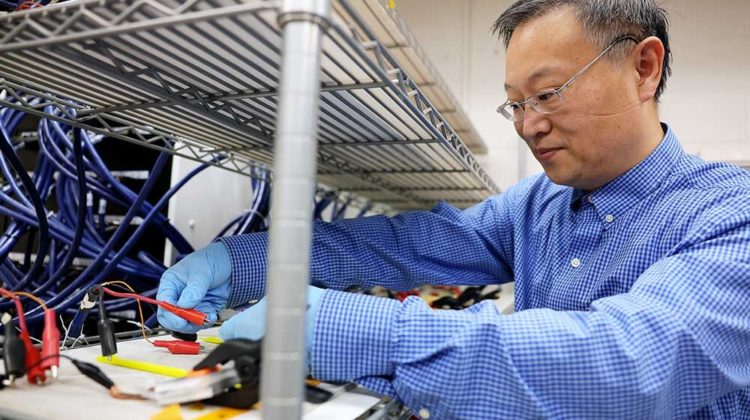
Researchers at the University of Michigan have developed a streamlined approach for testing electric vehicle battery designs that can drastically reduce the time it takes to assess how battery configurations will perform over the long haul, thus also reducing the cost.
‘The goal is to design a better battery and, traditionally, the industry has tried to do that using trial and error testing,’ said Wei Lu, a professor of mechanical engineering and leader of the research team behind the framework. ‘It takes such a long time to evaluate.’
The optimisation system developed by Lu’s team could cut the time for both simulation and physical testing of new and better batteries by about three quarters. That speed could provide a major boost to battery developers searching for the right combination of materials and configurations to ensure that consumers always have enough capacity to reach their destinations.
Parameters involved in battery design include everything from the materials used to the thickness of the electrodes and the size of the particles in the electrode. Testing each configuration usually means several months of fully charging and then fully discharging – known as cycling the battery – 1,000 times to mimic a decade of use. It’s extremely time-consuming to repeat this test through the huge number of possible battery designs to discover the better ones.
‘Our approach not only reduces testing time, but it automatically generates better designs,’ Lu said. ‘We use early feedback to discard unpromising battery configurations rather than cycling them till the end. This is not a simple task since a battery configuration performing mediocrely during early cycles may do well later on, or vice versa. We have formulated the early-stopping process systematically and enabled the system to learn from the accumulated data to yield promising new configurations.’
The U-M engineers harnessed the latest in machine learning to create a system that knows both when to quit and how to get better as it goes. The framework uses mathematical techniques known as Asynchronous Successive Halving Algorithm and Hyperband to figure out when to halt cycling tests that don’t get off to a promising start. Meanwhile, it takes data from previous tests and suggests new sets of promising parameters to investigate using Tree of Parzen Estimators.
In addition to cutting off tests that lack promise, a key time-saving element in U-M’s system is the fact that it generates multiple battery configurations to be tested at the same time, known as asynchronous parallelisation. If any configuration completes testing or is discarded, the algorithm immediately calculates a new configuration to test without the need to wait for the results of other tests.
U-M’s framework is effective in testing designs of all battery types, from those used for decades to run internal-combustion vehicles to the smaller products that power watches and mobile phones. However, EV batteries may represent the most pressing use of the technology.
‘This framework can be tuned to be more efficient when a performance prediction model is incorporated,’ said Changyu Deng, U-M doctoral student in mechanical engineering. ‘We expect this work to inspire improved methods that lead us to optimal batteries to make better EVs and other life-improving devices.’
‘By significantly reducing the testing time, we hope our system can help speed up the development of better batteries, accelerate the adoption or certification of batteries for various applications, and expedite the quantification of model parameters for battery management systems,’ Lu said.
The research has been published in Patterns-Cell Press.