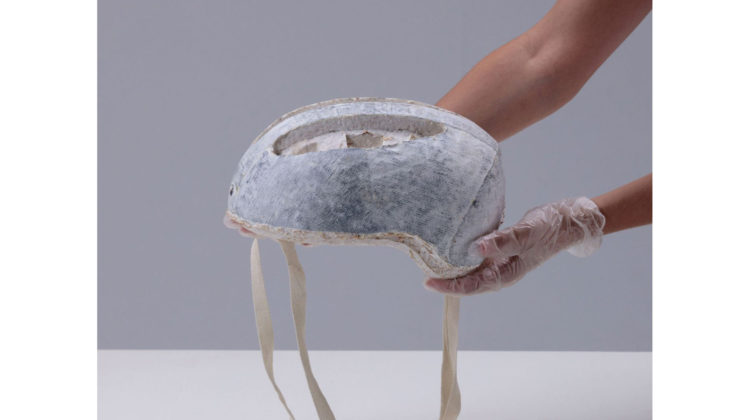
Dutch product and brand design group Studio MOM has developed a bicycle helmet made from natural materials that can be composted after use.
Junior designer Alessandra Sisti developed the helmet, dubbed MyHelmet, for her graduation project for the Masters programme in design and engineering at the Politecnico di Milano. MyHelmet features a main shell made from a specially developed form of mycelium – the fleshy root-like structure of a fungus – and an outer skin and strap produced from a hemp textile.
The design studio has been experimenting with bio-manufacturing based on mycelium and hemp flakes for some time. The mycelium used in the MyHelmet is the root network of a fungus that feeds on the flakes. Briefly heating the mycelium stops the growth process, resulting in a material that has properties similar to the expanded polystyrene foam used in conventional bicycle helmets.
The design team first made material samples in different compositions until they found the perfect composition.For the strap and outer shell, they used hemp textile, a biodegradable material to which the mycelium attaches itself. The different parts eventually grow together firmly – the strap is fixed during the growth process and connects to the other parts in the correct position,removing the need for glue.The woven structure of the hemp textile gives the helmet extra strength, while the natural layered structure of the mycelium allows for the airflow required to keep the wearer’s head cool.
For safety reasons, bicycle helmets must be replaced every three years, which creates a waste stream of a difficult-to-recycle, glued-together mixture of polystyrene foam and plastic. ‘MyHelmet fits in with principles of the circular economy: there are minimal CO2 emissions, it does not require any fossil raw materials and the end result is 100 per cent biodegradable,’ the studio said.
Studio MOM has carried out a series of initial tests, including a simulation of the NTA standards test – the test that determines whether or not a helmet complies with the requirements in the Dutch technical agreement – to ensure the product’s safety for use and is now looking for development partners.