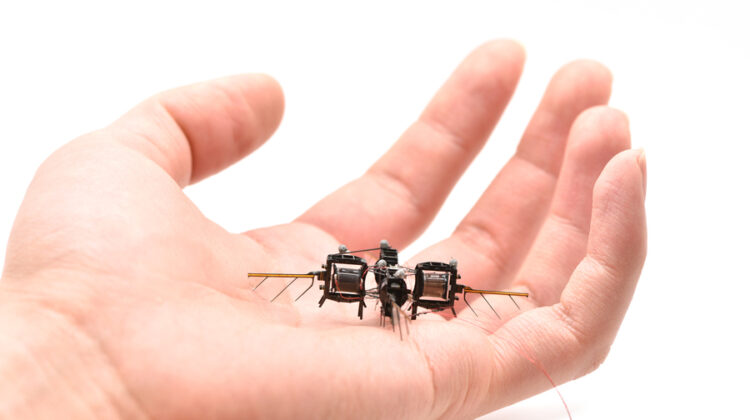
Researchers at MIT have developed tiny, aerial robots that are faster and far more agile and durable than prior versions.
The researchers hope that the robots could one day provide an efficient method for artificial pollination, enabling farmers to could grow fruits and vegetables inside multilevel warehouses, boosting yields while mitigating some of agriculture’s harmful impacts on the environment.
The new bots can hover for about 1,000 seconds, which is more than 100 times longer than previously demonstrated. The robotic insect, which weighs less than a paperclip, can also fly significantly faster than similar bots while completing acrobatic manoeuvres such as double aerial flips.
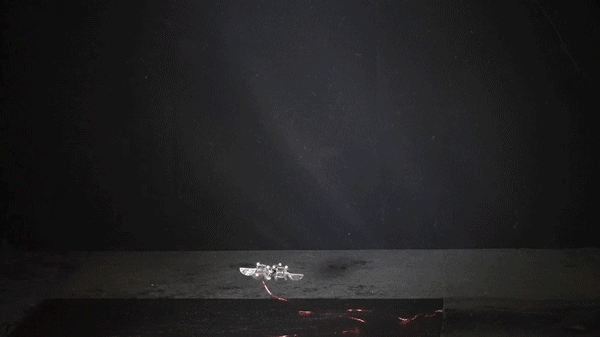
The new design boosts flight precision and agility while minimising the mechanical stress on the robot’s artificial wing flexures, which enables faster manoeuvres, increased endurance and a longer lifespan. There is also enough free space for the robot to carry tiny batteries or sensors, which could enable it to fly on its own outside the lab.
‘The amount of flight we demonstrated in this paper is probably longer than the entire amount of flight our field has been able to accumulate with these robotic insects. With the improved lifespan and precision of this robot, we are getting closer to some very exciting applications, like assisted pollination,’ said Kevin Chen, an associate professor in the Department of Electrical Engineering and Computer Science (EECS) and head of the Soft and Micro Robotics Laboratory within the Research Laboratory of Electronics (RLE),
Prior versions of the robotic insect were composed of four identical units, each with two wings, combined into a rectangular device about the size of a microcassette. ‘But there is no insect that has eight wings. In our old design, the performance of each individual unit was always better than the assembled robot,’ Chen said.
This performance drop was partly caused by the arrangement of the wings, which would blow air into each other when flapping, reducing the lift forces they could generate.
The new design chops the robot in half. Each of the four identical units now has one flapping wing pointing away from the robot’s centre, stabilising the wings and boosting their lift forces. With half as many wings, this design also frees up space so the robot could carry electronics.
In addition, the researchers created more complex transmissions that connect the wings to the actuators, or artificial muscles, that flap them. These durable transmissions, which required the design of longer wing hinges, reduce the mechanical strain that limited the endurance of past versions. ‘Compared to the old robot, we can now generate control torque three times larger than before, which is why we can do very sophisticated and very accurate path-finding flights,’ Chen said.
Yet even with these design innovations, there’s still a gap between the best robotic insects and the real thing. For instance, a bee has only two wings, yet it can perform rapid and highly controlled motions. ‘The wings of bees are finely controlled by a very sophisticated set of muscles. That level of fine-tuning is something that truly intrigues us, but we have not yet been able to replicate,’ Chen said.
The motion of the robot’s wings is driven by artificial muscles. These tiny, soft actuators are made from layers of elastomer sandwiched between two very thin carbon nanotube electrodes and then rolled into a squishy cylinder. The actuators rapidly compress and elongate, generating mechanical force that flaps the wings.
In previous designs, when the actuator’s movements reached the extremely high frequencies needed for flight, the devices often started to buckle, reducing the robot’s power and efficiency. The new transmissions inhibit this bending–buckling motion, which reduces the strain on the artificial muscles and enables them to apply more force to flap the wings.

Another new design involves a long wing hinge that reduces torsional stress experienced during the flapping-wing motion. Fabricating the hinge, which is about two centimetres long but just 200 microns in diameter, was among the team’s greatest challenges. ‘If you have even a tiny alignment issue during the fabrication process, the wing hinge will be slanted instead of rectangular, which affects the wing kinematics,’ Chen said. After many attempts, the researchers perfected a multistep laser-cutting process that enabled them to precisely fabricate each wing hinge.
With all four units in place, the new robotic insect can hover for more than 1,000 seconds, which equates to almost 17 minutes, without showing any degradation of flight precision. ‘When my student Nemo was performing that flight, he said it was the slowest 1,000 seconds he had spent in his entire life. The experiment was extremely nerve-racking,’ Chen said.
The new robot also reached an average speed of 35 centimetres per second, the fastest flight researchers have reported, while performing body rolls and double flips. It can even precisely track a trajectory that spells M-I-T. ‘At the end of the day, we’ve shown flight that is 100 times longer than anyone else in the field has been able to do, so this is an extremely exciting result,’ Chen said.
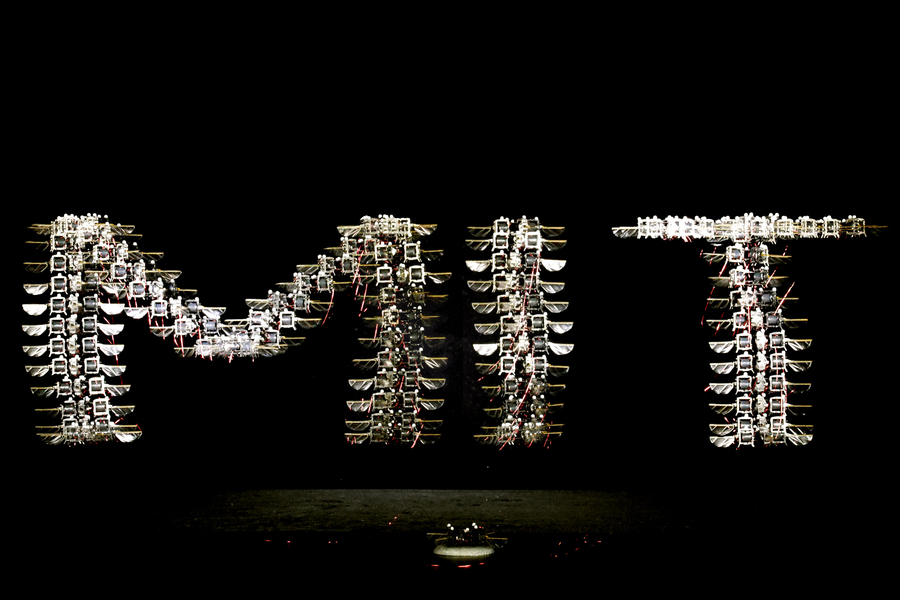
From here, Chen and his students want to see how far they can push this new design, with the goal of achieving flight for longer than 10,000 seconds. They also want to improve the precision of the robots so they can land and take off from the centre of a flower. In the long run, the researchers hope to install tiny batteries and sensors onto the aerial robots so they can fly and navigate outside the lab.
‘This new robot platform is a major result from our group and leads to many exciting directions. For example, incorporating sensors, batteries and computing capabilities on this robot will be a central focus in the next three to five years,’ Chen said.
The research has been published in Science Robotics.