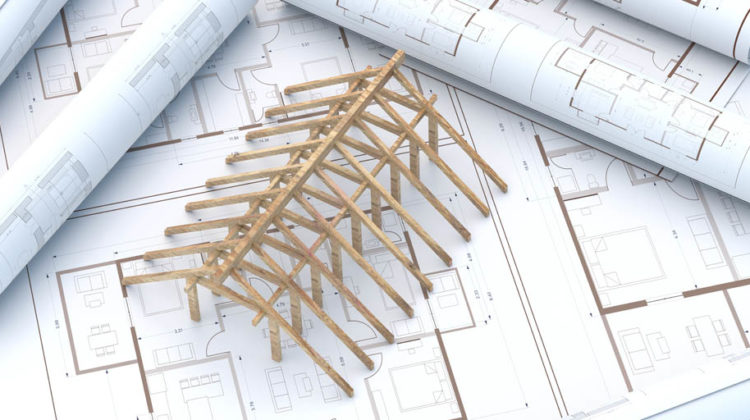
Architects and engineers will be better able to design truss structures in a way that minimises their embodied carbon thanks to a new set of computational tools developed by researchers at MIT.
A material or structure’s ‘embodied carbon’ factors in all of the carbon emitted during its production and use, including, for example, that from the fuel used for mining and smelting steel, or for felling and processing trees and in transporting the material to a site.
Truss structures – crisscross arrays of diagonal struts used for support in construction – are typically made of steel or wood or a combination of both. While in general wood has much less embodied carbon, using steel in places where its properties can provide maximum benefit can result in a smaller overall carbon footprint.
The MIT researchers carried out a detailed analysis of the different, often competing, factors involved and then created a set of computational tools that can be used to minimise the embodied carbon in truss structures while maintaining all of the properties required for a given building application. The tools can be applied at different stages, either in the early planning phase of a structure, or later on in the final stages of a design.
‘Construction is a huge greenhouse gas emitter that has kind of been flying under the radar for the past decades,’ said Josephine Carstensen, an assistant professor of civil and environmental engineering at MIT. However, building designers ‘are starting to be more focused on how to not just reduce the operating energy associated with building use, but also the important carbon associated with the structure itself.’
The two main options for reducing the carbon emissions associated with truss structures are substituting materials or changing the structure. But according to the researchers, there has been ‘surprisingly little work’ on tools to help designers figure out strategies for minimising emissions in a given situation.
The new system utilises a technique known as topology optimisation, in which a set of basic parameters, such as the amount of load to be supported and the dimensions of the structure, are used to produce designs that have been optimised for different characteristics, such as weight, cost, or, in this case, embodied carbon.
Using the optimisation tools to reengineer several trusses, the team demonstrated that an embodied carbon reduction of at least ten per cent was possible with no loss of performance. However, according to Carstensen, those estimates are ‘not exactly apples to apples’ and the savings could actually be two to three times greater.
‘It’s about choosing materials more smartly,’ Carstensen said. ‘There’s a big interest in the construction industry in mass timber structures and this speaks right into that area. So, the hope is that this would make inroads into the construction business and actually make a dent in that very large contribution to greenhouse gas emissions.’
The tools aren’t ready for commercial use as the researchers have yet to design a user interface.
The research has been published in Engineering Structures.