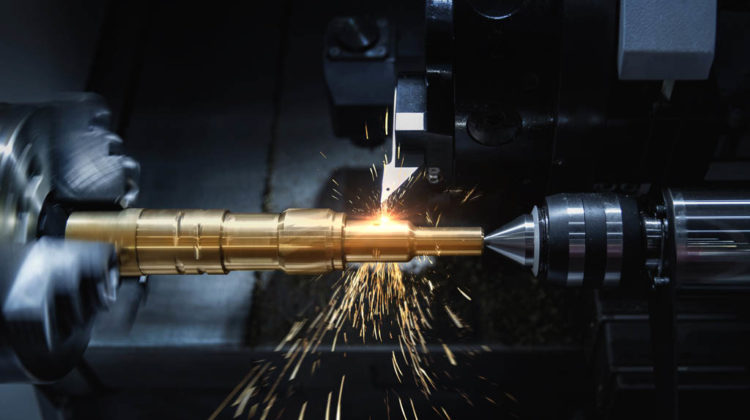
Researchers from Aarhus University in Denmark have developed an analytical model that explains how chips are formed during the milling process, enabling them to determine the perfect cutting process that minimises tool wear and optimises surface finish.
Many traditionalmanufacturing processes involve the shaping of components by removing chips from the surface of a bulk material; however, a clear understanding of the factors that control the size and shape of removed chips has remained elusive. This information is important because worn-out industrial milling tools and damaged materials cost the manufacturing industry billions each year.
‘We have developed a simple analytical model that can predict the mechanism for chip formation and its transition for almost every material,’ said Associate Professor Ramin Aghababaei, who is leading the research. ‘The model reveals the existence of a critical cutting depth as a function of material properties, tool geometry and running conditions.
‘By testing on various plastic materials, we have found a critical cutting depth, below which we can remove long chips in a smooth and gradual way, and above which, short and irregularly shaped chips formed in an abrupt manner,’ he continued. Deviation from this critical cutting depth has a major impact on the wear and tear of the tools used, energy consumption and the finish of the final product.
‘This breakthrough outcome is a result of having ambitious and professional partners in the project, and this achievement cannot be obtained without their individual contribution,’ Aghababaei said. ‘The team will continue to develop the model, but the tool industry can start using it already to design optimal cutting tools.’
The study has been published in Physical Review Letters.