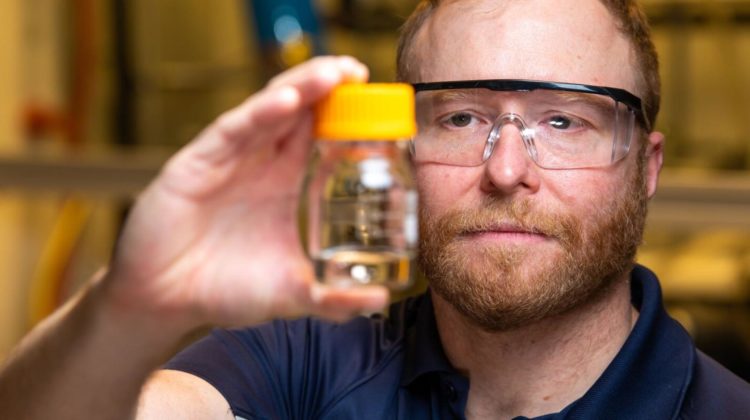
Scientists at the Department of Energy’s (DOE) Pacific Northwest National Laboratory (PNNL) have created a new system that captures carbon dioxide more cheaply than existing methods and converts it into one of the world’s most widely used chemicals: methanol.
The high cost of commercial carbon capture technology has been a longstanding barrier to its widespread use. The PNNL scientists believe that methanol can provide the incentive to adopt the technology. It holds many uses as a fuel and a solvent, and an important ingredient in plastics, paint, construction materials and car parts. Converting CO2 into useful substances such as methanol offers a path for industrial entities to capture and repurpose their carbon.
PNNL chemist David Heldebrant (pictured above) compares the system to recycling. Just as one can choose between single-use and recyclable materials, so too can one recycle carbon. ’That’s essentially what we’re trying to do here,’ he said. ‘Instead of extracting oil from the ground to make these chemicals, we’re trying to do it from CO2 captured from the atmosphere or from coal plants, so it can be reconstituted into useful things. You’re keeping carbon alive, so to speak, so it’s not just “pull it out of the ground, use it once and throw it away”. We’re trying to recycle the CO2, much like we try to recycle other things, such as glass, aluminium and plastics.’
The new system is designed to fit into coal-, gas-, or biomass-fired power plants, as well as cement kilns and steel plants. Using a PNNL-developed capture solvent, the system snatches CO2 molecules before they’re emitted, then converts them into useful, sellable substances.
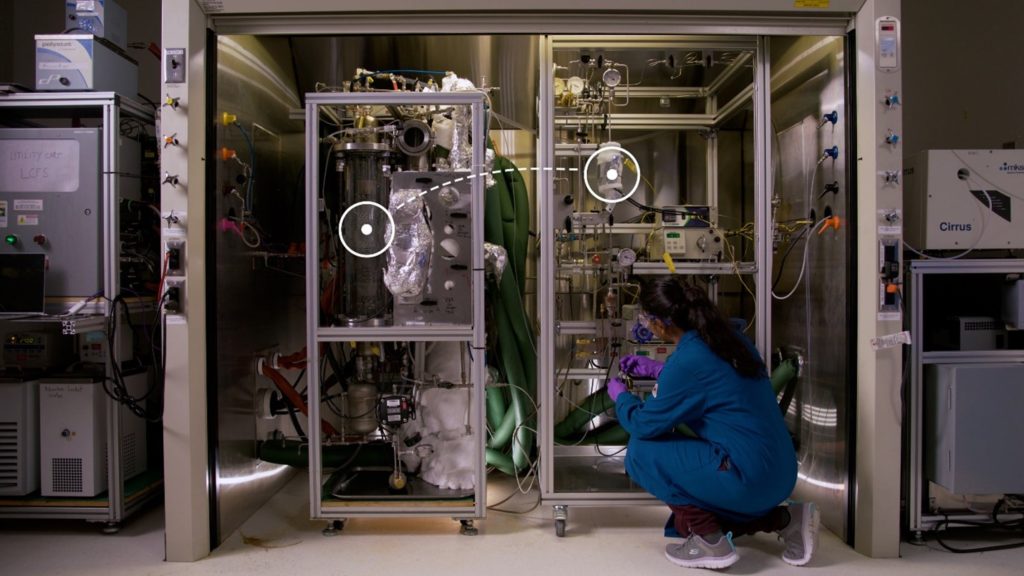
Deploying this technology will reduce emissions, said Heldebrant, but it could also help stir the development of other carbon capture technology and establish a market for CO2-containing materials. With such a market in place, carbon seized by anticipated direct air capture technologies could be better reconstituted into longer-lived materials.
By using renewably sourced hydrogen in the conversion, the team can produce methanol with a lower carbon footprint than conventional methods that use natural gas as a feedstock. Methanol produced via CO2 conversion could thus qualify for policy and market incentives intended to drive the adoption of carbon-reduction technologies.
Methanol is among the world’s most highly produced chemicals by volume. Known as a ‘platform material’, its uses are wide ranging. In addition to methanol, the team can convert CO2 into formate (another commodity chemical), methane and other substances.
According to a DOE analysis, existing commercial systems soak up carbon from flue gas at a cost of roughly US$46 per tonne of CO2. A new study in the Journal of Cleaner Production found that the cost of running the new methanol system is just below US$39 per tonne of CO2.
‘We looked at three CO2-binding solvents in this new study,’ said chemical engineer Yuan Jiang. ‘We found that they capture more than 90 per cent of the carbon that passes through them, and they do so for roughly 75 per cent of the cost of traditional capture technology.’
While creating methanol from CO2 isn’t new, the ability to both capture carbon and then convert it into methanol in one continuously flowing system is. Capture and conversion have traditionally occurred as two distinct steps, separated by each process’s unique, often non-complementary chemistry. ‘We’re finally making sure that one technology can do both steps and do them well,’ said Heldebrant, adding that traditional conversion technology typically requires highly purified CO2. The new system is the first to create methanol from ‘dirty’ CO2.
The process of capturing CO2 and converting it to methanol isn’t CO2-negative. The carbon in that methanol is released when burned or sequestered when methanol is converted to substances with longer lifespans. But this technology does ‘set the stage’, Heldebrant said, for the important work of keeping carbon bound inside material and out of the atmosphere.
The research has been published in Advanced Energy Materials.