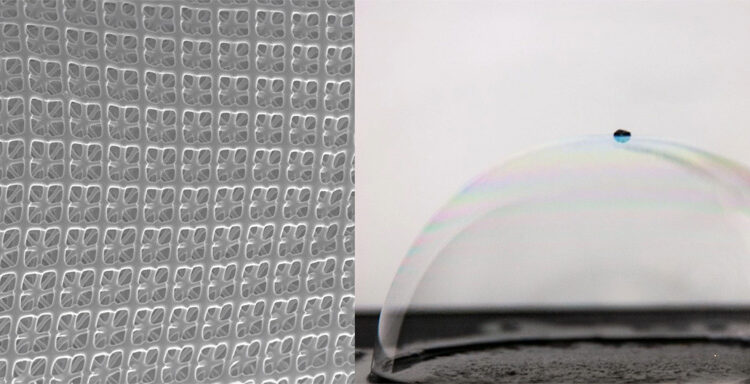
Researchers from the University of Toronto’s Faculty of Applied Science and Engineering have used machine learning to design nano-architected materials that have the strength of carbon steel but the lightness of Styrofoam.
The new nanomaterials’ properties offer a conflicting combination of exceptional strength, light weight and customisability. According to the researchers, their approach could benefit a wide range of industries, from automotive to aerospace.
‘Nano-architected materials combine high-performance shapes, like making a bridge out of triangles, at nanoscale sizes, which takes advantage of the “smaller is stronger” effect to achieve some of the highest strength-to-weight and stiffness-to-weight ratios, of any material,’ said Peter Serles. ‘However, the standard lattice shapes and geometries used tend to have sharp intersections and corners, which leads to the problem of stress concentrations. This results in early local failure and breakage of the materials, limiting their overall potential. As I thought about this challenge, I realised that it is a perfect problem for machine learning to tackle.’
Nano-architected materials are made of tiny building blocks or repeating units measuring a few hundred nanometres in size – it would take more than 100 of them patterned in a row to reach the thickness of a human hair. These building blocks, which in this case are composed of carbon, are arranged in complex 3D structures called nanolattices. The image above shows the full lattice geometry juxtaposed with an 18.75-million cell lattice floating on a bubble.
To design their improved materials, Serles and Professor Tobin Filleter worked with Professor Seunghwa Ryu and PhD student Jinwook Yeo at the Korea Advanced Institute of Science and Technology (KAIST) in Daejeon, South Korea. This partnership was initiated through U of T’s International Doctoral Clusters programme, which supports doctoral training through research engagement with international collaborators.
The KAIST team employed the multi-objective Bayesian optimisation machine-learning algorithm. This algorithm learned from simulated geometries to predict the best possible geometries for enhancing stress distribution and improving the strength-to-weight ratio of nano-architected designs.
Serles then used a two-photon polymerisation 3D printer housed in the Centre for Research and Application in Fluidic Technologies to create prototypes for experimental validation. This additive manufacturing technology enables 3D printing at the micro and nano scale, creating optimised carbon nanolattices.
These optimised nanolattices more than doubled the strength of existing designs, withstanding a stress of 2.03 megapascals for every cubic metre per kilogram of its density, which is about five times higher than titanium.
‘This is the first time machine learning has been applied to optimise nano-architected materials, and we were shocked by the improvements,’ said Serles. ‘It didn’t just replicate successful geometries from the training data; it learned from what changes to the shapes worked and what didn’t, enabling it to predict entirely new lattice geometries.
‘Machine learning is normally very data intensive, and it’s difficult to generate a lot of data when you’re using high-quality data from finite element analysis,’ he continued. ‘But the multi-objective Bayesian optimisation algorithm only needed 400 data points, whereas other algorithms might need 20,000 or more. So, we were able to work with a much smaller but an extremely high-quality data set.’
‘We hope that these new material designs will eventually lead to ultra-lightweight components in aerospace applications, such as planes, helicopters and spacecraft that can reduce fuel demands during flight while maintaining safety and performance,’ said Filleter. ‘This can ultimately help reduce the high carbon footprint of flying.’
‘For example, if you were to replace components made of titanium on a plane with this material, you would be looking at fuel savings of 80 litres per year for every kilogram of material you replace,’ added Serles.
‘This was a multi-faceted project that brought together various elements from material science, machine learning, chemistry and mechanics to help us understand how to improve and implement this technology,’ said Serles, who is now a Schmidt Science Fellow at the California Institute of Technology.
‘Our next steps will focus on further improving the scale-up of these material designs to enable cost effective macroscale components,’ adds Filleter. ‘In addition, we will continue to explore new designs that push the material architectures to even lower density while maintaining high strength and stiffness.’
The research has been published in Advanced Materials.