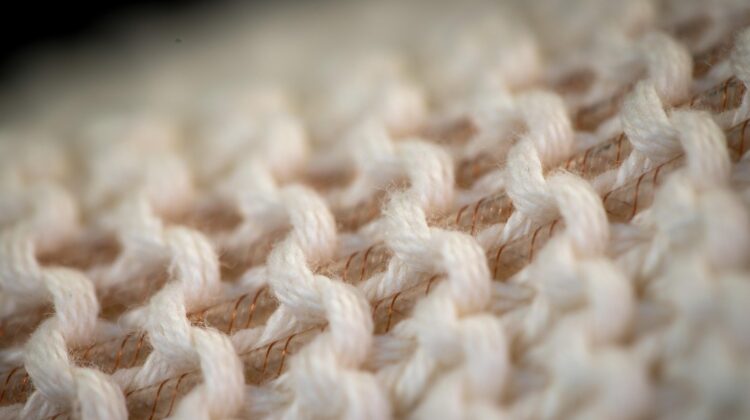
Researchers from the Ecole Polytechnique Fédérale de Lausanne (EPFL) have developed fibre-like pumps that allow high-pressure fluidic circuits to be woven into textiles without an external pump. Soft supportive exoskeletons, thermoregulatory clothing and immersive haptics can therefore be powered from pumps sewn into the fabric of the devices themselves.
Many fluid-based wearable assistive technologies today require a large and noisy pump that is impractical – if not impossible – to integrate into clothing. This leads to a contradiction: wearable devices are routinely tethered to unwearable pumps. Now, however, researchers in the Soft Transducers Laboratory (LMTS) in EPFL’s School of Engineering have developed an elegantly simple solution to this dilemma.
‘We present the world’s first pump in the form of a fibre; in essence, tubing that generates its own pressure and flow rate,’ said LMTS head Herbert Shea. ‘Now, we can sew our fibre pumps directly into textiles and clothing, leaving conventional pumps behind.’
In 2019, Shea’s lab produced the world’s first stretchable pump. ‘This work builds on our previous generation of soft pump,’ said Michael Smith, an LMTS post-doctoral researcher. ‘The fibre format allows us to make lighter, more powerful pumps that are inherently more compatible with wearable technology.’
The fibre pumps use a principle called charge injection electrohydrodynamics to generate a fluid flow without any moving parts. Two helical electrodes embedded in the pump wall ionise and accelerate molecules of a special non-conductive liquid. The ion movement and electrode shape generate a net forward fluid flow, resulting in silent, vibration-free operation and requiring just a palm-sized power supply and battery.
To achieve the pump’s unique structure, the researchers developed a novel fabrication technique that involves twisting copper wires and polyurethane threads together around a steel rod and then fusing them with heat. After the rod is removed, the two-millimetre-diameter fibres can be integrated into textiles using standard weaving and sewing techniques.
The pump’s simple design has a number of advantages. The materials required are cheap and readily available, and the manufacturing process can be easily scaled up. Because the amount of pressure generated by the pump is directly linked to its length, the tubes can be cut to match the application, optimising performance while minimising weight. The robust design can also be washed with conventional detergents.
The researchers have suggested several ways in which these fibre pumps can be used in wearable technologies. For example, they can circulate hot and cold fluid through garments for those working in extreme-temperature environments or in a therapeutic setting to help manage inflammation; and even for those looking to optimise athletic performance.
‘These applications require long lengths of tubing anyway, and in our case, the tubing is the pump. This means we can make very simple and lightweight fluidic circuits that are convenient and comfortable to wear,’ Smith said.
Work has begun on scaling up the production of the fibre pumps, and the LMTS also has plans to embed them into more complex wearable devices. ‘We believe that this innovation is a game-changer for wearable technology,’ Shea said.
The research has been published in Science.