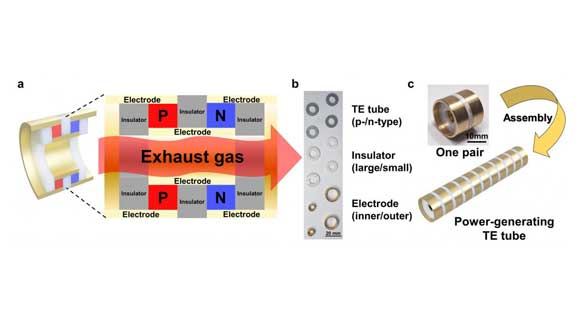
A team of engineers affiliated with UNIST in Ulsan, South Korea’s largest industrial city, have developed a new thermoelectric technology that can be used to produce power-generating tubes using 3D printing techniques. The researchers suggest that the technology could open the way for generating electricity from waste heat produced by factories and cars and other vehicles.
By turning waste heat into electricity, thermoelectric technologies can enhance efficiencies and reduce fuel consumption. However, at present, most thermoelectric solutions are relatively expensive and ineffective.
The researchers found that using a tube-shaped device is more effective than conventional devices, which are typically based around parallelepiped shapes (a parallelepiped is a three-dimensional figure formed by six parallelograms). Drawing on these findings, they created a thermoelectric tube using a 3D-printed ink made from lead and tellurium. Particles of the metal particles were mixed with a glycerol solvent, creating a viscoelastic substance – that is, it exhibits both viscous and elastic characteristics. The resultant tube was found to have a high thermoelectric performance at temperatures of between 400C and 800C, which is the typical temperature range of a car’s exhaust gases.

‘Through this research, we will be able to effectively convert heat generated by factory chimneys, the most common type of waste heat source, into electricity,’ said Professor Jae Sung Son from the Department of Materials Science and Engineering at UNIST, who jointly led the study.
‘If we use 3D printing technology in the production of thermoelectric materials, we will be able to overcome limits of conventional materials,’ said Professor Han Gi Chae, who also led the study. ‘The new technology for providing viscoelastic characteristics to 3D printed materials will be used in various other sectors.’
The results of the study have been published in Advanced Energy Materials.