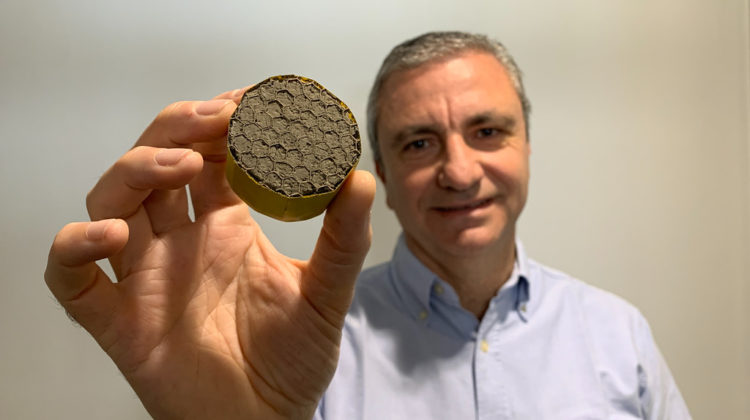
A team of researchers at the University of Bath has developed a new lightweight material that could significantly reduce the engine noise produced by aircraft.
Weighing just 2.1 kilograms per cubic metre, the graphene oxide-polyvinyl alcohol aerogel is the lightest sound-insulating material ever manufactured.‘We managed to produce such an extremely low density by using a liquid combination of graphene oxide and a polymer, which are formed with whipped air bubbles and freeze-casted,’ said Michele Meo, a professor in the Department of Mechanical Engineering’s Materials and Structures Centre, who led the research. ‘On a very basic level, the technique can be compared with whipping egg whites to create meringues – it’s solid but contains a lot of air, so there is no weight or efficiency penalty to achieve big improvements in comfort and noise.’
Despite its extremely low density, the material has extremely impressive sound-absorbing capabilities.Over the 400–2500 Hz range, the material’s average sound absorption coefficients are as high as 0.79.
The aerogel’s combination of low density with excellent sound absorption makes it ideal as an insulator within aircraft engine nacelles – external housings – where it would reduce noise with almost no increase in overall weight. The average reduction in sound transmission can be as high as 16 decibels, which would mean that the 105-decibel roar of a jet engine taking off would be closer to that of a hairdryer.
The material is also effectively ‘tuneable’; changes to the environmentally friendly manufacturing process used to produce it affect its acoustic properties, so it could potentially be made to order to increase the absorption of particular frequencies of sound. The researchers suggest that it may also have fire resistance and electromagnetic-shielding properties.
‘This is clearly a very exciting material that could be applied in a number of ways – initially in aerospace but potentially in many other fields such as automotive and marine transport, as well as in building and construction,’ Meo said.
A method for manufacturing the material has been published in the journal Nature Scientific Reports. The team estimates that it could be in use within 18 months.