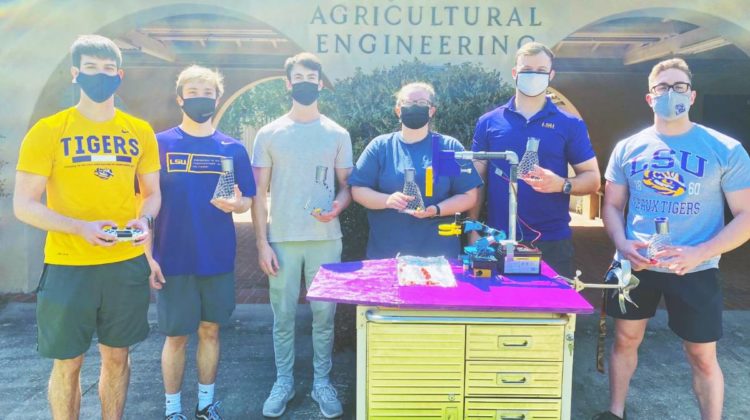
A team of six senior students from Louisiana State University’s Department of Biological and Agricultural Engineering has designed a semi-autonomous robotic arm for use in the harvesting of crawfish. According to the team, the arm could save workers time and money, and also prevent back injuries.
Each year, between the months of March and June, hundreds of harvesters collect more than 44,000 tonnes of crawfish in South Louisiana. Each harvester works alone in a boat, forcing them to drive with a foot while simultaneously picking up, emptying and rebaiting traps.
‘I don’t think there’s anything wrong with the way crawfish are currently harvested, but if there’s a possibility to improve the way we are harvesting, we should try,’ said engineering student Ben Thomas. ‘The main reason to build the arm is to improve speed, which would increase productivity. Most agricultural production is trying to be automated to increase yield, and with the growth of the crawfish industry, we thought we’d give it a try.’
‘Due to COVID, I could not find a suitable graduate student in 2020, so I decided to put a group of senior design students to work on a miniature prototype,’ said Professor Chandra Theegala, who has a grant from the United States Department of Agriculture to begin development of mechanical and automated harvesting for crawfish producers. ‘I limited the scope to a small robotic arm that is commercially available. Each student focused on a particular component of the project.’
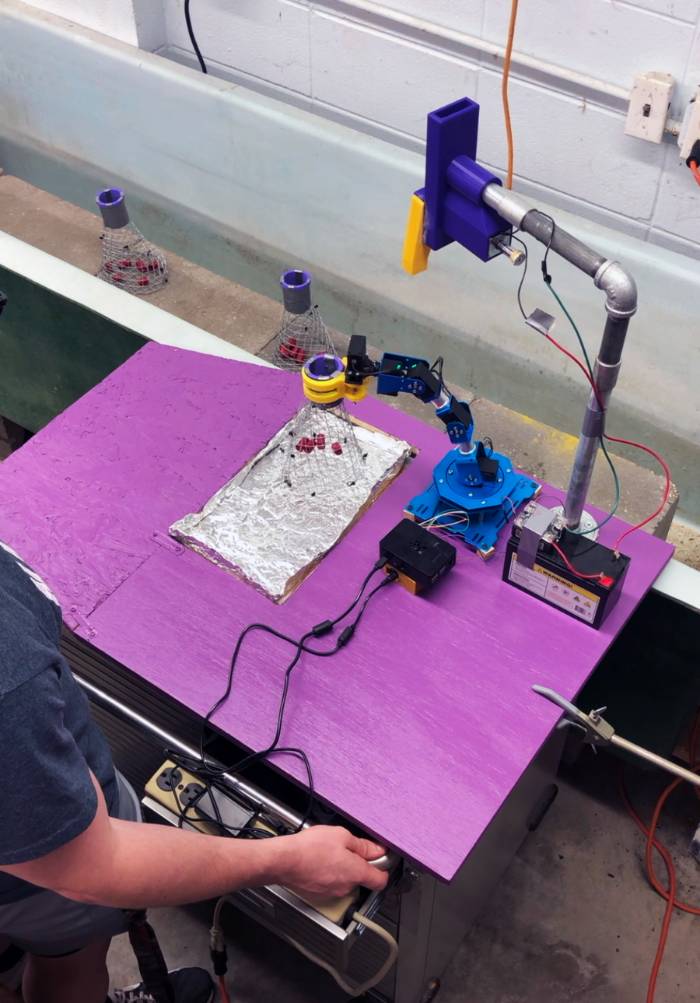
The students built the harvesting arm to one third the scale of a commercial crawfish trap, programming it to work partially autonomously, fabricating a trap-rebaiting system, and designing and 3D printing a custom gripper. Using a Playstation 4 controller, it’s possible to direct the arm to grab a trap. The rest of the process – tipping out the crustaceans, rebaiting the trap and putting it back into position – is autonomously controlled.
‘The hope is to have it be entirely autonomous, being able to align itself on a moving boat,’ Thomas said.
According to the team’s test results, the design is 88 per cent reliable at picking up traps, at an average of 18.3 seconds, which is roughly as fast as a person.
‘If the arm could be fully autonomous, the grabbing time could be reduced by a significant amount since, in an ideal situation, the boat would never stop and the arm’s reach would be able to grab the trap towards the front of the boat,’ Thomas said.
‘This project was especially exciting to me because I know the impact it could potentially have on my own crawfish farm in the future,’ said David Vercher, who also worked on the project. ‘We all had impeccable teamwork skills that allowed us to work together efficiently. I couldn’t have asked for a better team.’