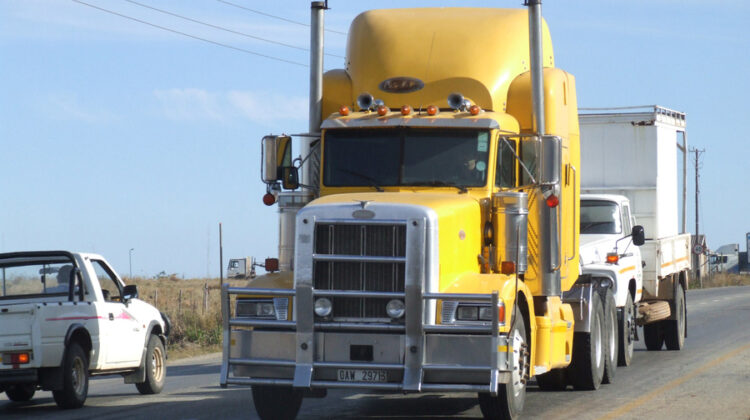
A new study by MIT researchers has quantified the impact that the design of a zero-emission truck has on its energy storage requirements and operational revenue. The multivariable model they developed allows fleet owners and operators to better understand the design choices that affect the economic feasibility of battery-electric and hydrogen fuel cell heavy-duty trucks for commercial applications, equipping stakeholders with the ability to make informed fleet transition decisions while also underscoring the need for cross-sector collaboration.
‘The whole issue [of decarbonising trucking] is like a very big, messy pie. One of the things we can do, from an academic standpoint, is quantify some of those pieces of pie with modelling, based on information and experience we’ve learned from industry stakeholders,’ said ZhiYi Liang, a PhD student on the renewable hydrogen team at MIT K Lisa Yang Global Engineering and Research Center (GEAR).
The team’s research elucidates the operational and socioeconomic factors that need to be considered in efforts to decarbonise heavy-duty vehicles (HDVs). Their model shows that a technical challenge lies in the amount of energy that needs to be stored on the truck to meet the range and towing performance needs of commercial trucking applications. Due to the high energy density and low cost of diesel, existing diesel drivetrains remain more competitive than alternative lithium battery-electric vehicle (Li-BEV) and hydrogen fuel-cell-electric vehicle (H2 FCEV) drivetrains. Although Li-BEV drivetrains have the highest energy efficiency of all three, they are limited to short- to medium-range routes (under 800 kilometres) with low freight capacity, due to the weight and volume of the onboard energy storage needed. In addition, the researchers note that existing electric grid infrastructure will need significant upgrades to support large-scale deployment of Li-BEV HDVs.
While the hydrogen-powered drivetrain has a significant weight advantage that enables higher cargo capacity and routes of more than 1,000 kilometres, the current state of hydrogen fuel networks limits economic viability, especially once operational cost and projected revenue are taken into account. Deployment will most likely require government intervention in the form of incentives and subsidies to reduce the price of hydrogen by more than half, as well as continued investment by corporations to ensure a stable supply. Also, as H2-FCEVs are still a relatively new technology, the ongoing design of conformal onboard hydrogen storage systems – one of which is the subject of Liang’s PhD – is crucial to successful adoption into the HDV market.
The current efficiency of diesel systems is a result of technological developments and manufacturing processes established over many decades, a precedent that suggests similar strides can be made with alternative drivetrains. However, interactions with fleet owners, automotive manufacturers and refuelling-network providers reveal another major hurdle in the way that each ‘slice of the pie’ is interrelated – issues must be addressed simultaneously because of how they affect each other, from renewable fuel infrastructure to technological readiness and capital cost of new fleets, among other considerations. And first steps into an uncertain future, where no one sector is fully in control of potential outcomes, is inherently risky.
‘Besides infrastructure limitations, we only have prototypes [of alternative HDVs] for fleet operator use, so the cost of procuring them is high, which means there isn’t demand for automakers to build manufacturing lines up to a scale that would make them economical to produce,’ said Liang, describing just one step of a vicious cycle that is difficult to disrupt, especially for industry stakeholders trying to be competitive in a free market.
‘Folks in the industry know that some kind of energy transition needs to happen, but they may not necessarily know for certain what the most viable path forward is,’ says Liang. Although there is no singular avenue to zero emissions, the new model provides a way to further quantify and assess at least one slice of pie to aid decision-making.
While current limitations reveal the need for joint problem-solving across sectors, the researchers believe that stakeholders are motivated and ready to tackle climate problems together. Once-competing businesses already appear to be embracing a culture shift toward collaboration, as evidenced by the recent agreement between General Motors and Hyundai to explore ‘future collaboration across key strategic areas’, including clean energy.
Liang believes that transitioning the transportation sector to zero emissions is just one part of an ‘energy revolution’ that will require all sectors to work together, because ‘everything is connected. In order for the whole thing to make sense, we need to consider ourselves part of that pie, and the entire system needs to change,’ said Liang. ‘You can’t make a revolution succeed by yourself.’
Details of the research can be found here.